Porosity in Welding: Identifying Common Issues and Implementing Ideal Practices for Avoidance
Porosity in welding is a prevalent issue that usually goes unnoticed till it causes substantial problems with the honesty of welds. This common problem can endanger the strength and longevity of welded frameworks, posing security threats and resulting in pricey rework. By understanding the root creates of porosity and executing reliable avoidance techniques, welders can dramatically improve the high quality and integrity of their welds. In this conversation, we will explore the vital factors contributing to porosity formation, analyze its destructive effects on weld performance, and talk about the very best techniques that can be embraced to lessen porosity occurrence in welding procedures.
Common Causes of Porosity
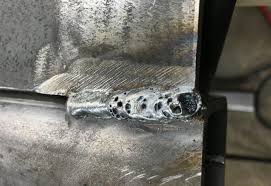
Utilizing filthy or damp filler products can present impurities into the weld, contributing to porosity problems. To alleviate these typical reasons of porosity, detailed cleansing of base steels, correct securing gas selection, and adherence to optimal welding parameters are crucial methods in attaining high-quality, porosity-free welds.
Influence of Porosity on Weld Quality

The visibility of porosity in welding can considerably compromise the structural stability and mechanical residential properties of bonded joints. Porosity produces spaces within the weld metal, weakening its total toughness and load-bearing capability. These gaps function as anxiety concentration points, making the weld extra prone to splitting and failure under used tons. Additionally, porosity can reduce the weld's resistance to rust and other ecological aspects, even more diminishing its long life and performance.
Welds with high porosity levels have a tendency to show reduced influence strength and decreased capability to warp plastically prior to fracturing. Porosity can impede the weld's ability to properly transfer forces, leading to early weld failure and prospective safety risks check here in essential structures.
Best Practices for Porosity Prevention
To improve the architectural integrity and high quality of bonded joints, what particular actions can be executed to decrease the occurrence of porosity during the welding procedure? Using the right welding strategy for the specific material being bonded, such as readjusting the welding angle and weapon position, can additionally protect against porosity. Regular evaluation of welds and prompt removal of any kind of issues identified during the welding procedure are crucial techniques to prevent porosity and produce premium welds.
Relevance of Correct Welding Techniques
Executing appropriate welding methods is vital in making certain the architectural honesty and top quality of bonded joints, constructing upon the structure of reliable porosity avoidance actions. Welding strategies straight influence the total toughness and longevity of the bonded structure. One essential element of appropriate welding techniques is maintaining the correct heat input. Too much warmth can cause boosted porosity because of the entrapment of gases in the weld pool. Alternatively, not enough warmth may result in insufficient blend, producing potential weak points in the joint. In addition, making use of the proper welding parameters, such as voltage, existing, and travel speed, is crucial for attaining sound welds with minimal porosity.
In addition, the choice of welding process, whether it be MIG, TIG, or stick welding, need to line up with the particular requirements of the project to ensure ideal outcomes. Proper cleansing and prep work of the base metal, in addition to picking the appropriate visit here filler material, are additionally important parts of competent welding methods. By sticking to these best methods, welders can lessen the threat of porosity formation and create premium, structurally audio welds.
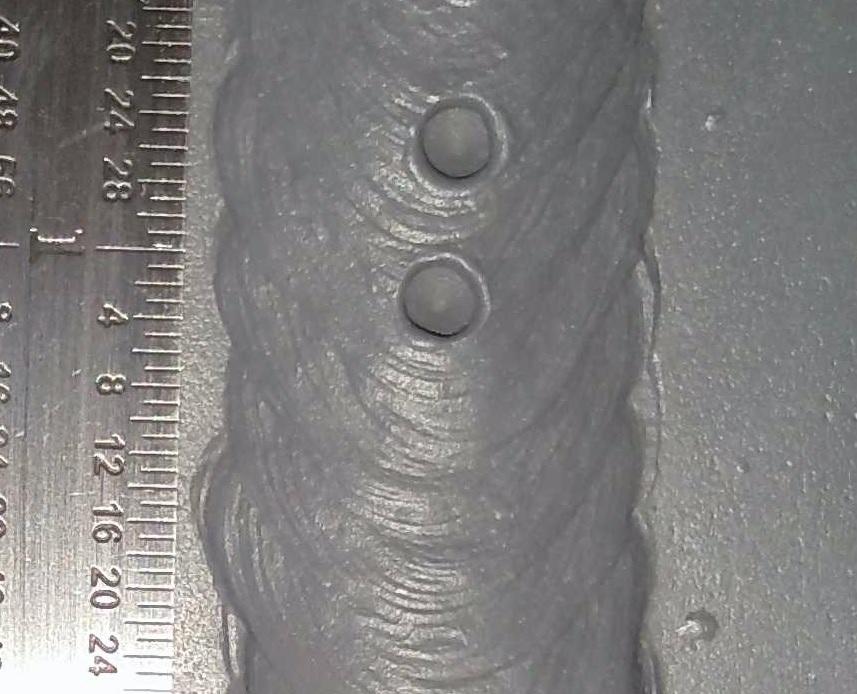
Evaluating and Top Quality Control Actions
Quality control procedures play a critical duty in verifying the integrity and reliability of welded joints. Checking procedures are necessary to detect and avoid porosity in welding, ensuring the toughness and toughness of the end product. Non-destructive testing methods such as ultrasonic testing, radiographic testing, reference and visual inspection are commonly employed to recognize possible issues like porosity. These strategies permit the evaluation of weld high quality without endangering the honesty of the joint. What is Porosity.
Post-weld examinations, on the various other hand, assess the final weld for any problems, including porosity, and confirm that it satisfies specified requirements. Carrying out a detailed high quality control plan that includes complete screening procedures and assessments is vital to minimizing porosity problems and making sure the general high quality of welded joints.
Conclusion
To conclude, porosity in welding can be a common concern that influences the high quality of welds. By determining the common sources of porosity and applying ideal methods for prevention, such as proper welding strategies and screening procedures, welders can make sure premium quality and dependable welds. It is important to focus on avoidance methods to minimize the event of porosity and preserve the integrity of bonded structures.